We have previously published a guide to power station control room. Many people have asked how to design a power plant control room. As a professional control room console manufacturer, we hope that our practical experience below will be helpful to you.
I. Why the Power plant Control Room Really Matters
If you’ve ever stepped into a power station, you know the power plant control room isn’t just another part of the building. It’s the brain. This is where operators monitor turbines, manage grid output, respond to alarms, and make fast, often critical decisions. When things start to go sideways, this is where the response kicks in.
But that only works if the power plant control room is designed right.
I’ve been part of power plant control room design projects for years, and one thing is always true: every plant is different. What works at a gas-fired facility probably won’t fly in a nuclear one. That’s why cookie-cutter layouts don’t cut it. You need a setup built around your plant’s specific risks, workflows, and layout. This is supported by case studies in the power industry, such as the work done at Singleton Birch, where a customized control room design was implemented to meet the specific needs of the plant’s operational processes and safety concerns (Thinking Space, 2024).
And no, it’s not just about throwing in fancy monitors or expensive chairs. It’s about creating a space that helps people do their jobs better. Think about things like comfortable seating, clear sightlines, glare-free lighting, and low noise levels. Every detail matters when your team is making split-second calls.
And here’s the thing—you need to plan for change. What happens when you upgrade your systems? Or bring in new teams? Or face new regulations? If your power plant control room can’t adapt, you’re stuck with costly retrofits later.
So yeah, the power plant control room matters. Get it right, and your operators have the tools and environment they need to perform at their best. Cut corners, and you’re taking risks with safety, reliability, and performance.
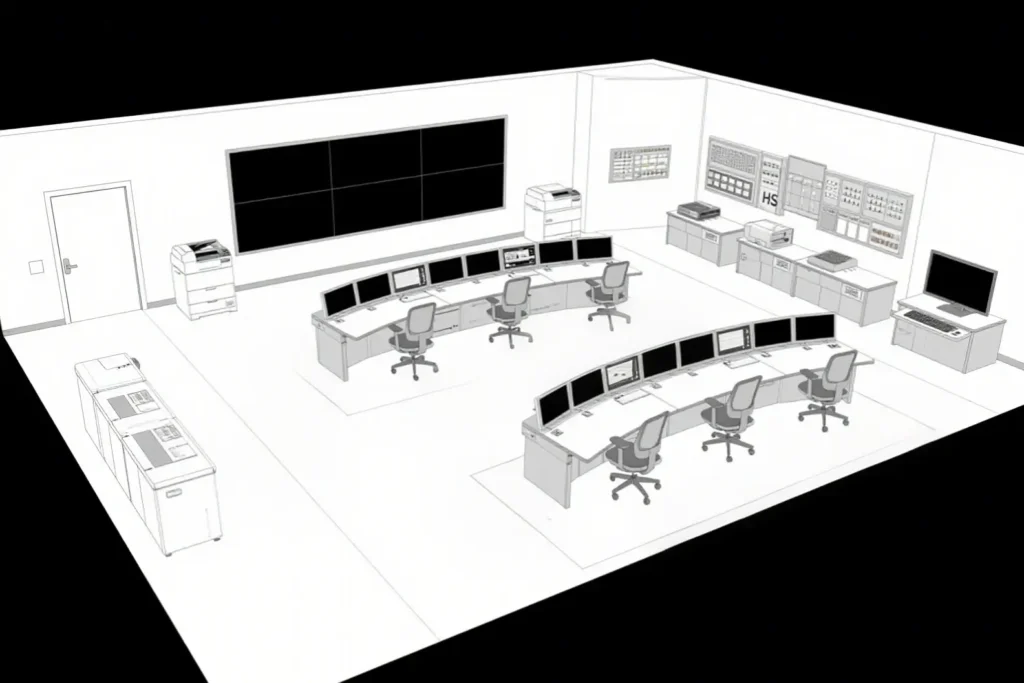
II. Building for Safety from the Start
Let’s talk safety. Power plants are inherently high-risk. So the power station control room? It needs to be the safest spot in the place. Not just secure—resilient.
We always start with the big threats. Fire, explosions, gas leaks—whatever could happen, the power plant control room has to be ready. That might mean reinforced concrete walls, blast-resistant windows, or even sealing the room completely with pressurized air systems to keep contaminants out.
In hazardous plants, the power control room often doubles as a refuge. So we plan for that too. Think emergency exits (more than one), vestibules that act like airlocks, and backup systems for power, lighting, and communications. We’ve even seen setups with breathing equipment for long emergencies. Smart, honestly.
And all of this is grounded in real standards. ISO 11064 is a solid baseline for power plant control room design and safety. But we never stop there. Every facility has unique risks, and your design should reflect that. As noted by MECART (2022), these design elements are crucial for power stations, where control rooms need to be designed with features such as blast-resistant windows and emergency systems to ensure safety during hazardous situations (MECART, 2022).
Bottom line: a good power station control room doesn’t just survive an emergency. It lets your team keep working through one. That’s what you really need.
III. Designing Around the Operator
Now, let’s shift focus to the people actually working in the room. Because the best tech in the world won’t help if the layout wears your team down.
Operators spend long hours at consoles, juggling complex systems and high-stress decisions. The power control room should work with them, not against them.
Start with the basics: visibility and reach. Screens should sit where the eyes naturally fall. Controls should be where your hands expect them to be. We group related equipment so folks aren’t spinning around chasing different systems. When time matters, that efficiency adds up.
Comfort is a big deal, too. Lighting should hit that sweet spot—500 to 800 lux per ISO 8995. Bright, but not blinding. Flicker-free and adjustable is the goal. Sound matters as well. We use acoustic panels and absorbent materials to bring background noise below 85 dB(A), in line with OSHA guidance. And climate? Cool, stable air keeps fatigue from creeping in during long shifts.
Teamwork is a big piece of today’s power plant control room design. That’s why we lean toward U-shaped or open layouts with shared screens. When everyone sees the same thing, collaboration gets easier.
And it helps to have a small nearby area for quick meetings or shift handovers. That way, operators can huddle without disrupting the core workflow.
When operators feel physically and mentally supported, performance improves. That’s the difference between a room full of equipment and a true command center. The importance of ergonomic design in control rooms, which includes appropriate lighting, seating, and noise control, is discussed by Tresco Consoles (2024), emphasizing how these factors significantly improve operator well-being and efficiency in high-stress environments (Tresco Consoles, 2024).
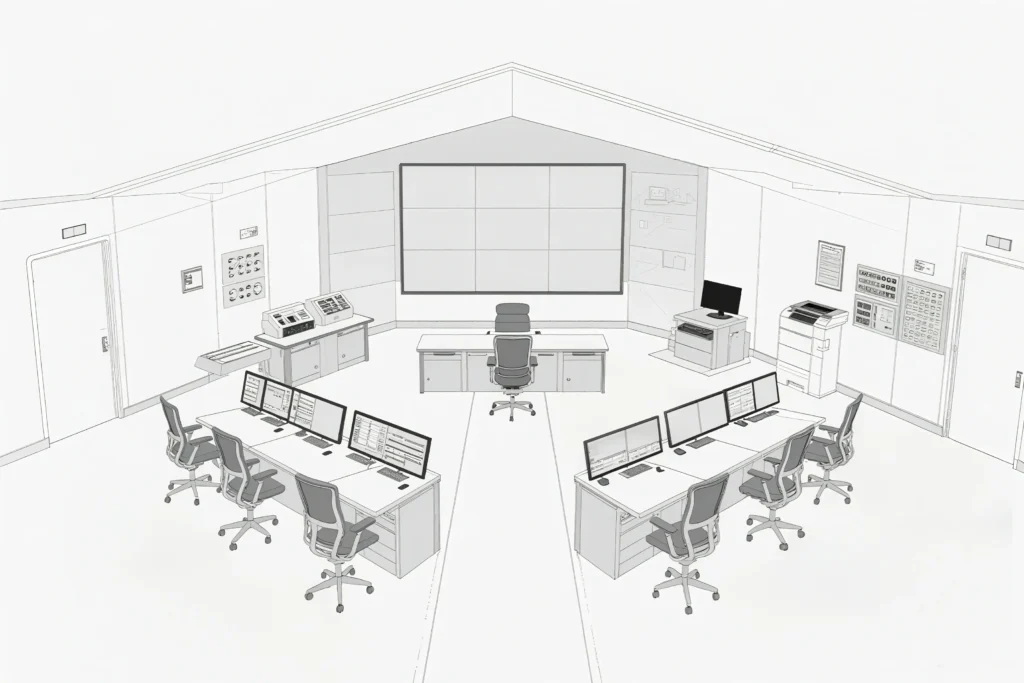
IV. Planning for the Future, Not Just Today
Here’s something we see a lot: power station control rooms built for today that fall short tomorrow.
Plants evolve. Tech moves fast. Teams grow. Rules change. If your power control room can’t flex, you’re going to hit walls—literally and figuratively.
Start with a layout that’s easy to adapt. Open-plan spaces give you visibility and flexibility. Modular setups are great if you need to reconfigure teams or equipment down the line. In a modern power plant control room, flexibility is key to keeping up with changing technologies and growing operations.
The way teams interact should shape the layout. Maybe it’s parallel rows for specialized roles. Maybe circular pods for tight coordination. Whatever fits your workflow best.
We also plan ahead with infrastructure. That means extra conduit, accessible cable trays, and flexible power/data routes. Leave space for more screens, more servers, and future tools. When it’s time to bring in new systems, you won’t need to tear the place apart.
Also think about capacity. Can this space support remote monitoring later? Hybrid operations? A bigger team during peak demand? You don’t need to predict the future—just be ready for it.
V. Why Custom Work Makes the Difference
No two plants are alike. So why would their power station control rooms be?
We’ve worked on coal plants with major dust exposure, nuclear sites with strict shielding needs, and everything in between. The risks are different. The operators are different. The workflows are different. Custom power plant control room design lets you build for that reality.
With a custom approach, you can line up your layout with your process. Build in the right safety features. Design a space that feels natural to work in. One that fits your team.
Off-the-shelf designs? They often end up costing more later. Sure, they’re quick to drop in. But making changes after the fact? Painful and expensive. A custom power plant control room design bakes in flexibility from day one.
One of the biggest wins? Getting your team involved early. Operators, engineers, safety staff—they know what works. Their feedback shapes a better room. One where people move naturally, communicate easily, and know exactly what to do when things get tense.
We also document everything—from layout logic to upgrade plans—so when it’s time to evolve, you’re not starting from scratch.
A well-designed power plant control room doesn’t just check the boxes. It mirrors how your plant actually runs. It supports your team. And it’s ready for whatever comes next.
Do you want to custom power control rooms? Feel free to contact us — a power control room manufacturer.